|
ACCESS THE FULL ARTICLE
No SPIE Account? Create one
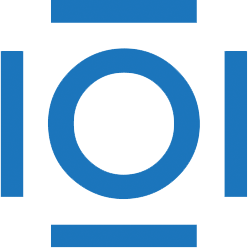
CITATIONS
Cited by 2 scholarly publications.
Surface roughness
Tungsten
Radium
Diamond machining
Single point diamond turning
Precision glass molding
Process modeling