|
ACCESS THE FULL ARTICLE
No SPIE Account? Create one
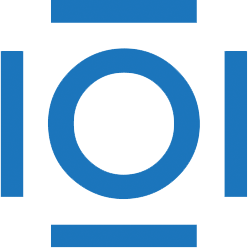
CITATIONS
Cited by 52 scholarly publications.
Composites
Shape memory polymers
Prototyping
Structural design
Aluminum
Carbon
Data modeling