Optical lithography has been undisputedly the current generation lithography ever since the invention of the integrated circuit in 1958. After half a century, with minimum half pitch reduced from 1500 to , its ending is finally in sight. Succeeding optical lithography while maintaining Moore’s law is a tremendous challenge for the next-generation lithography (NGL). What lithography will handle features smaller than and is extendable for a few more generations? In terms of energy higher than that from 193-nm radiation, the possibilities are 13.5-nm x ray, electron beam, and ion beam; in terms of capability to replicate nanometer-size features, nanoimprint technology using an intimately contacting mold is a possibility. What is the prospect of these candidates becoming the NGL? The most popular candidate, EUV (13.5-nm x ray), has attracted the most attention and funding. Plenty of articles on EUV have been published in the last decade. Even this editor has written an article in on it. In view of the uncertainty and the prospect of unacceptable wafer manufacturing cost, is there any other technology that can sustain the cost of single-exposure optical immersion lithography, use an equivalent or smaller footprint for the same productivity, consume less wall power, and reverse the mask cost escalation trend? Table 1 shows the relative tool, exposure, processing, and material costs of a water-immersion single-exposure system, a double-patterning water-immersion system, an EUV system at , and two multiple-electron-beam direct-write systems at 20 and each. The cost are normalized to the first system. The estimation includes tool utilization, availability, rework, installation, utility, laser pulse, resist, HMDS, developer, topcoat, BARC, and etching, wherever applicable. Table 1Cost comparison.
The cost target of a NGL can be derived from Table 1 and is shown in Table 2 . If either an ion-beam or a nano-imprint tool mimics the exposure + processing + material cost of the MEB system, then any of them will be worth the price shown, according to their throughput. Since the cost of the single-exposure system is based on the previous generation, there is some allowance for the NGL generation. Hence, the 20-wph tool can command between 10 and ; the 40-wph tool, . The footprint of a typical scanner is where the hardware occupies . The remaining area is required for tool access and the light source assembly is placed on the subfloor. Hence, the NGL tool has to fit the same space per , i.e., a 20-wph tool has to cluster five of the exposure units into , while allowing subfloor space for remote-access parts such as the data processing equipment for maskless tools. Can each exposure unit fit into approximately ? With 5X lower throughput and scanning schemes that either minimize or eliminate stage acceleration and deceleration, it is reasonable to expect NGL stage speed on the order of , against on optical scanners. Thus, the smaller footprint is feasible. Table 2NGL target cost.
If a maskless NGL tool meets these requirements, mask cost, cycle time, elimination of the mask contribution to the CD control and overlay budgets, and no requirement on pellicles will be bonuses. With comparable manufacturing cost at any number of wafers per mask, there will be a demand for this NGL tool no matter whether the product is logic, flash, or DRAM. Moore’s law will march on. Happy reading! |
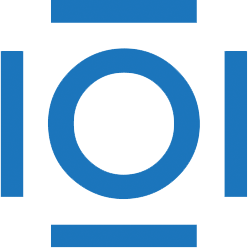
CITATIONS
Cited by 5 scholarly publications.